Hirotaka Sato was in Tokyo when the earthquake struck in March 2011. The tremors destroyed tens of thousands of buildings and triggered a tsunami that battered Japan’s east coast, including the Fukushima nuclear power plant. More than 18,000 people died or were never found. As Sato watched desperate search-and-rescue missions unfold, he thought, “I need to develop the technology to save people.”
The solution he soon envisaged — and which has occupied him ever since — was a cyborg insect. He imagined a swarm of live creatures scurrying through the rubble, controlled when necessary by remotely operated electrodes implanted in the insects’ nervous systems. The creatures would carry mounted sensors capable of identifying survivors, along with transmitters to signal their location to rescue workers.
Sato — now an engineer at Nanyang Technological University in Singapore — has chosen the Madagascar hissing cockroach (Gromphadorhina portentosa) as the basis for his rescue squad. These 5-centimetre-long creatures can carry up to 15 grams of mounted technology, which currently includes an infrared camera and a processor capable of detecting living people. Sato’s team can remotely steer the insects left, right and forwards, or leave them to autonomously navigate to programmed destinations1. The researchers are now refining the tracking and communication systems required for the cyborg creatures to be able to tell rescuers where to find people who are in need of help.
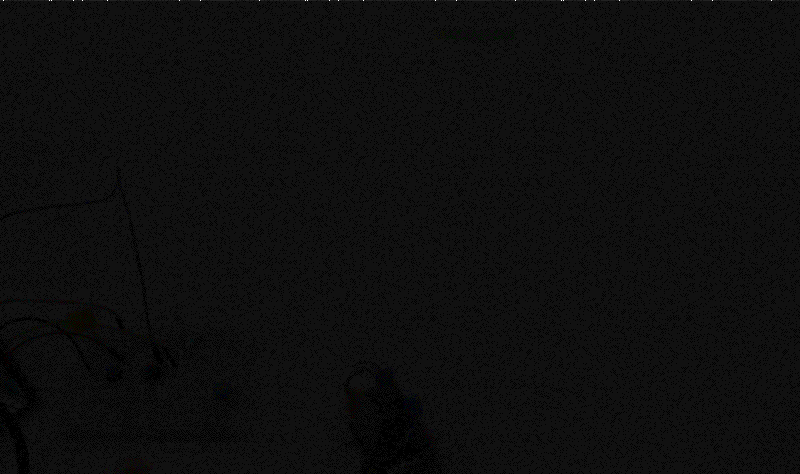
Sato’s laboratory is one of dozens around the world working in the emerging field of biohybrid robotics — a discipline in which engineers seek to make robots from a combination of conventional metal and plastic components, and living biological tissues. “A biohybrid is really any robot that combines both biological materials and synthetic materials,” says Victoria Webster-Wood, an engineer at Carnegie Mellon University in Pittsburgh, Pennsylvania.
The type and amount of biological material used vary considerably between researchers — as do the challenges they are aiming to resolve. With cyborgs such as Sato’s search and rescue cockroaches, roboticists harness the natural capabilities of largely intact biological systems. In other cases, researchers are exploring how small amounts of living tissue — an odour-sensing moth antenna2, for instance, or a covering of human skin3 — might serve specific functions in otherwise conventional robots. Some of the most ambitious projects place living cells at the core of robot designs, such as those seeking to construct powerful, self-healing muscles that a robot can use to move.
Despite their differing approaches, most of the researchers involved have a shared interest in harnessing nature to advance robotics. But as those working in the field know all too well, serious obstacles still stand in the way of bringing biohybrid robots fully to life.
Harnessing nature
In early 2011, Sato was finishing off a four-year stint in the lab of Michel Maharbiz at the University of California, Berkeley. Sato’s work, funded by the US Defense Advanced Research Projects Agency (DARPA), had sought to sidestep the difficulties of building centimetre-scale flying robots from scratch by instead controlling live flying beetles (Mecynorrhina torquata) with tiny on-board computers4. Hijacking the beetles’ natural abilities not only bypassed the engineering challenge of flight, but also yielded cyborgs that were self-powered and in possession of a sophisticated sensory system to help navigate the world.Part of Nature Outlook: Robotics and artificial intelligence
When the Tohoku earthquake struck, it took only a small conceptual leap — substituting flying beetles with scuttling cockroaches — for Sato to envisage a cyborg that could move through the rubble of razed buildings. Rescue workers have long used dogs (and their remarkable sense of smell) to search hazardous earthquake sites. Engineers have been developing robots to do likewise for decades. However, like dogs, when confronted with mountains of rubble, most robots are restricted to traversing the surface. Exploring inside would require something smaller and hardier — more like a cockroach.
Sato’s intention is to use hundreds of cyborg cockroaches to autonomously explore search zones. But to ensure they remain in the target area, Sato needed a means of directing their movement.
He did this by attaching electrodes to parts of the insect’s body, which can be controlled by either a remote human operator or the on-board computer. Electrically stimulating touch receptors or muscles on a cockroach’s left side makes the insect move right, and vice versa. “We use the insect’s natural behaviour to induce a turn,” says Sato. Stimulating left and right movements simultaneously propels the cockroach forward. The group’s latest prototypes use navigation algorithms, run by an on-board computer, to control the insect’s direction according to what the infrared camera detects1. Obstacle avoidance is achieved by monitoring the cockroach’s motion — if it is brought to a stop by an obstacle, the navigation algorithm will direct the insect to move away from the blockage and find a way around it.
A cyborg cockroach navigates autonomously through obstacles. Audible beeps indicate the detection of a human. Credit: P. T. Tran-Ngoc etal. Adv. Intell. Syst. 5, 2200319 (2023).
Sato points out that small fully synthetic robots — development of which is advancing quickly — could move through similar environments. But cyborg insects could have a major advantage: operating time.
“We can put only a small battery on a small robot,” Sato says. Because that battery must power a robot’s energy-hungry locomotive system, as well as their payload devices, he says, “artificial robots can move only for few minutes”. Conversely, cyborg insects power their movement by eating and drinking, meaning small on-board batteries need to fuel only the vision and communication systems, and the low-wattage devices that steer the insects.
His team’s latest prototypes have operating times of around eight hours, but Sato hopes this can be extended considerably in future by harvesting energy for the payload from the sun5 or from the insects’ haemolymph6 — an invertebrate equivalent of blood. He hopes to deploy these biohybrid machines in disaster zones in the next 3–5 years.
Sato is not alone in developing animal cyborgs. Nicole Xu, an engineer at the University of Colorado Boulder, spent her PhD in the lab of engineer John Dabiri, then at Stanford University, California, and now based at the California Institute of Technology (Caltech) in Pasadena. Together they explored ways to control how jellyfish swim. The goal, explains Xu, is to use swarms of sensor-carrying jellyfish to monitor the effects of climate change and other ecological shifts in large expanses of ocean.
Jellyfish use a pumping action to swim — a ring of nerves cause their body to contract, which propels them forward. Xu showed that by attaching an electrode to a jellyfish using a wooden toothpick and stimulating the nerve ring in a certain pattern, she could make the animal swim nearly three times faster than normal7.
Cyborg jellyfish can be made to swim against a constant flow of water that unmodified jellyfish do not resist. Credit: Nicole W. Xu and John O. Dabiri
To test whether the cyborg creations stood up to ocean conditions, they were dropped from a boat off the coast of Massachusetts8. The jellyfish still swam at elevated speeds. “That was really nice,” Xu says, “because we got a sense of the waves and how hardy these robots were.”
Jellyfish have a number of appealing characteristics for roboticists. They are energy-efficient swimmers, and are able to descend to great depths. Compared with current mechanical submersibles, Xu says, jellyfish are less likely to cause damage to marine environments. Their natural appearance and quietness also make them unremarkable — during the ocean tests, fish swam right up to them.
The cyborg jellyfish are at a much earlier stage of development than Sato’s cockroaches, and are being refined by the Dabiri lab at Caltech. Tasks ahead include finding a way to direct the animals rather than simply speeding them up, and establishing what sensors — such as cameras or chemical probes — they can carry without impacting their buoyancy. Keeping in communication with such deep-water cyborgs also presents a challenge.
Biohybrid jellyfish robots released into the sea could help to monitor the effects of climate change. Credit: N. W. Xu etal. Biomimetics5, 64 (2020).
Intelligent design
Co-opting intact bodies and nervous systems of animals has advantages over building a robot from scratch, but using nature’s creations so completely also imposes limitations. “Whenever we’re hijacking an existing organism, we are limited to the functionalities and the body-form factors that evolution has resulted in,” says Webster-Wood. She and other researchers are instead aiming to use biological materials as building blocks in robots of their own design — machines that will be engineered to excel at specific applications.
So far, most of this work has used muscle. When choosing what kind of actuator to use in a robot design, Webster-Wood explains, roboticists consider various metrics, including the amount of force it generates relative to its weight, energy efficiency and durability. Although muscle does not score the highest on any one metric, it does score well across many. “Existing actuators have some serious limitations,” Webster-Wood says. “Especially for small-scale robots.”
For instance, several types of electric motor — such as piezoelectric motors — can change stiffness and shape, but it is difficult to scale them down to the same size as a small muscle. And such motors require sizable batteries.
Biological muscle also has properties that synthetic actuators do not currently offer. Ritu Raman, a mechanical engineer at the Massachusetts Institute of Technology in Cambridge, has built centimetre-scale robots by combining skeletal muscle cells derived from mice with synthetic hydrogel scaffolding. When the muscle cells are made to contract by electrical stimulation or — after genetic modification — by pulses of light, these machines propelled themselves around a Petri dish9.
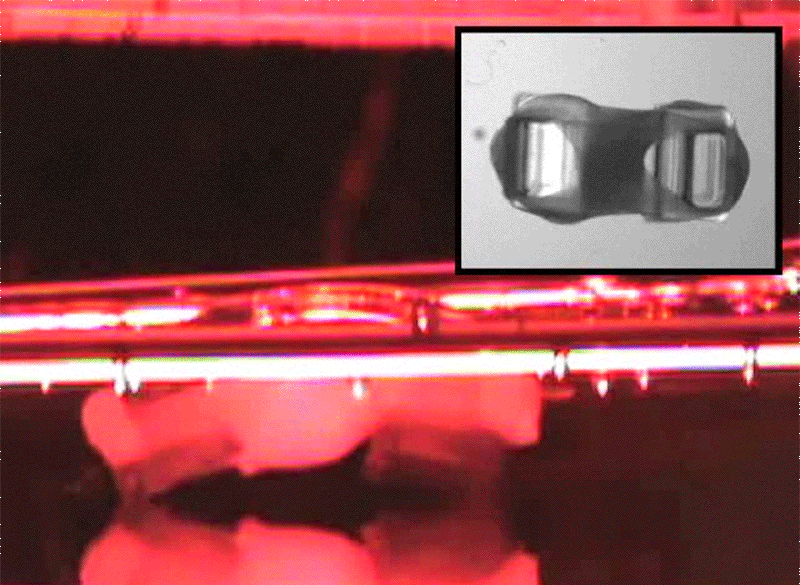
The more often Raman stimulated the robots, the more force the muscles generated each time — similar to a person training to lift heavier weights. Such strengthening could be useful if it enabled robots to become better at tasks that they repeated in the real world.
Strikingly, Raman also showed that if the muscle were cut, and then stem cells and growth factors added, the biohybrid bots healed10. “It could completely restore the force that it was producing and the speed at which it was walking within a couple days,” she says. Her plan is for future designs to incorporate stem cells from the start, to enable self-healing.
In a bid to gain finer control over their movement, Raman is now developing muscle systems connected to neurons that can trigger contraction, just as they exist in animals. In the longer term, she aims to use networks of biological neurons that can sense external stimuli as well, enabling them to move in response to environmental cues.
Another major draw of using biological materials is that they naturally degrade — as well as being safe to eat, should a predator consume them. “We are all-in on biodegradable,” says Webster-Wood. She says that robotics researchers have a basic responsibility to think about the components they use and the fate of those materials when their robots are not recovered. Indeed, as well as the living muscle cells she uses, Webster-Wood is also exploring the use of natural proteins for the robots’ structural and electrical components.
Like Xu, Webster-Wood is keen to develop ways of monitoring aquatic ecosystems, such as the development of toxic algal blooms in the Great Lakes between the United States and Canada. For this task, the muscle tissue she is testing has an important advantage over the mouse-derived muscle used by Raman and others: it comes not from mammals, whose muscles must be kept roughly at body temperature in custom-made nutritive solutions, but rather from Aplysia californica sea slugs — animals she describes as “super robust”.
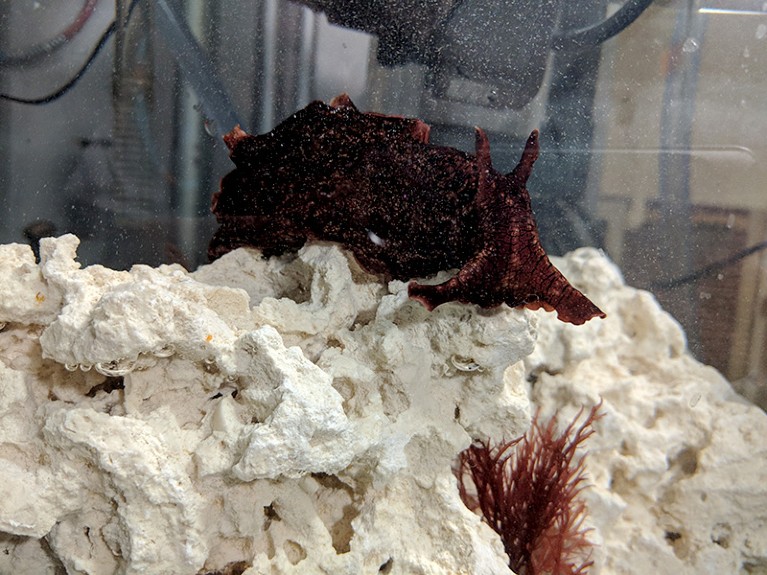
Webster-Wood says that Aplysia muscle can operate across a wider range of environmental conditions than can fragile mammalian muscle. After all, these sea slugs live in tidal rock pools and experience huge changes in temperature and salinity. When testing her biohybrid creations in artificial ocean water — which would kill mammalian tissues almost instantly — Webster-Wood has seen them function for around an hour11. However, an environmental-monitoring robot would probably need to function for much longer to be useful, so there is still some work to be done to improve their longevity.
A means to an end?
Not everyone creating biohybrid robots has to worry about how their creation will hold up in the field, however. “I look at biohybrid robotics as an experimental tool,” says Kit Parker, a biomedical engineer who studies cardiac disease at Harvard University in Boston, Massachusetts. “That’s how I get to understand the heart.”
Around 14 years ago, Parker went with his daughter to the New England Aquarium in Boston. He was frustrated then — as he is now — with how many clinical cardiology trials were failing, and he increasingly thought this was due to a basic shortcoming: “We don’t understand the fundamental laws of muscular pumps,” he says.
Standing before a tank of jellyfish, he thought, “Wow, that thing is pumping just like a heart.” Then, came a second thought: “I bet I can build that.”
In a landmark biohybrid paper12 published in 2012, he and his colleagues did just that. The team described mapping the architecture of a jellyfish, building a small synthetic skeleton, then seeding it with cardiomyocytes — the muscle cells of the heart, which intrinsically and rhythmically contract and relax. The results were centimetre-long replica jellyfish that swam around pools of culture medium. “I learnt so much,” he says.
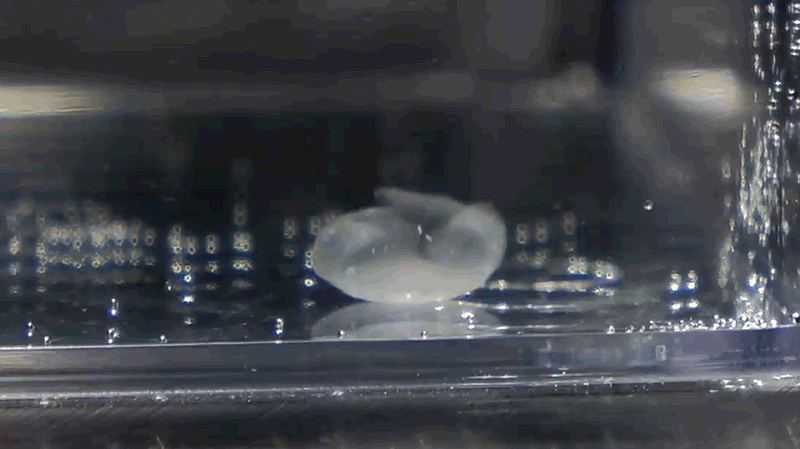
Last year, Parker’s group unveiled some small biohybrid fish made of cardiomyocytes13. Studying how the fish generated their rhythmic movements challenged long-held assumptions about how the pace-making node of the heart works, revealing how layers of heart cells communicate to create rhythmicity. It was a similar story in 2016, when the team demonstrated miniature cardiomyocyte rays14, closer in shape to stingrays and skates. Parker says that the pulsing, turning movements of these robotic rays provided insights into why the anatomy of the heart is the way it is.
Parker views his biohybrid robots as way stations en route to his goal of engineering treatments for dysfunctional hearts. “I’m a bioengineer and I build things out of heart cells,” he says. “If we want to move towards building pieces of heart,” he adds, “you have to understand the cell as a building material.”
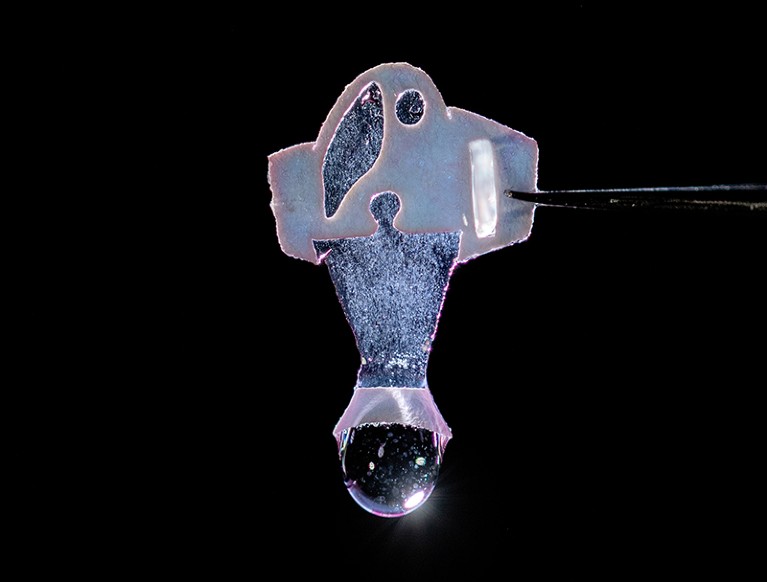
He is not alone in seeing the utility of biohybrid robots as research tools. Xu says that cyborg jellyfish could enable investigations into the biology of these animals, and Raman says combining neurons with muscles might help to create models of neuromuscular diseases. She has also experimented with grafting the light-sensitive muscle tissue she has been working with back into injured mice, to accelerate their recovery15.
The long haul
Parker’s biohybrid bots fulfilled the ambitions he had for them: they were made and lived in a laboratory, and they allowed him to answer scientific questions. The question that looms for other biohybrid roboticists is whether these machines can fulfil more alluring, broader visions.
There are numerous issues with biohybrid robotics that need to be addressed for biological tissues and systems to become a more common sight in roboticists’ creations, says Webster-Wood. “A lot of the tissue-engineering-based biohybrid robotics is still at the basic research level,” she says.
As well as making biohybrid creations tough enough to survive in the wild, it is uncertain to what extent muscle-based systems can be made larger than the 1–2-centimetre size that is currently achievable. Such a development might require something similar to vascularizing the tissues, so that all cells receive the energy and nutrients they need. On this point, Raman is buoyed by her work with muscle grafts, in which stimulating muscular contraction seemed to encourage the growth of blood vessels and nerves in injured mice. “Perhaps exercise can be used to accelerate the growth of blood vessels and make things that can be chunkier,” she says.
But perhaps the biggest issue concerns scaling up production. Until now, most biohybrid robots have been essentially handmade. Raman says devices made by different people, even in the same lab, often vary — as do robots made with different batches of cells. “That’s a huge issue,” she says. To start addressing reliable large-scale production, Raman’s lab is now working on 3D-printing approaches.
Stingray-like biohybrid robots containing cardiomyocytes were engineered to follow a light source. Credit: Disease Biophysics Group, Harvard University
Parker does not mince his words in his appraisal of biohybrid efforts so far: “It’s arts and crafts, it’s not engineering,” he says. Behind each of his high-profile robotic-fish papers, he says, there were years spent learning how to build with cardiac muscle cells. To understand how to bind muscle cells to synthetic backbones, his team used equations describing the physical properties of the backbone materials, to make approximations of how the system would behave. “You’ve got to have design tools,” Parker says. ”Otherwise, these are just party tricks.”
Sato’s ambition is to build much more than a simple party trick, however. “Our motivation is purely to use this technology for search and rescue,” he says. “To save people from disaster.”
As for Raman, she is in this for the long haul. “Maybe it will take us a couple of decades to get something that can function outside of a Petri dish,” she says. “I’m just very comfortable with 30-year goals.”
doi: https://doi.org/10.1038/d41586-023-03801-0
References
- Tran-Ngoc, P. T. et al. Adv. Intell. Syst. 5, 2200319 (2023).Article Google Scholar
- Anderson, M. J., Sullivan, J. G., Horiuchi, T. K., Fuller, S. B. & Daniel, T. L. Bioinspir. Biomim. 16, 026002 (2020).Article Google Scholar
- Kawai, M., Nie, M., Oda, H., Morimoto, Y. & Takeuchi, S. Matter 5, 2190–2208 (2022).Article Google Scholar
- Sato, H. et al. Curr. Biol. 25, 798–803 (2015).Article PubMed Google Scholar
- Kakei, Y. et al. npj Flex. Electron. 6, 78 (2022).Article Google Scholar
- Shoji, K. et al. Biosens. Bioelectron. 78, 390–395 (2016).Article PubMed Google Scholar
- Xu, N. W. & Dabiri, J. O. Sci. Adv. 6, eaaz3194 (2020).Article PubMed Google Scholar
- Xu, N. W. et al. Biomimetics 5, 64 (2020).Article PubMed Google Scholar
- Raman, R. et al. Proc. Natl Acad. Sci. USA 113, 3497–3502 (2016).Article PubMed Google Scholar
- Raman, R. et al. Adv. Healthcare Mater. 6, 1700030 (2017).Article Google Scholar
- Webster, V. A. et al. In Biomimetic and Biohybrid Systems. Living Machines 2017 Vol. 10384 (eds Mangan, M. et al.) 475–486 (Springer, 2017).Google Scholar
- Nawroth, J. C. et al. Nature Biotechnol. 30, 792–797 (2012).Article PubMed Google Scholar
- Lee, K. Y. et al. Science 375, 639–647 (2022).Article PubMed Google Scholar
- Park, S.-J. et al. Science 353, 158–162 (2016).Article PubMed Google Scholar
- Rousseau, E. et al. Biomaterials 302, 122317 (2023).Article PubMed Google Scholar