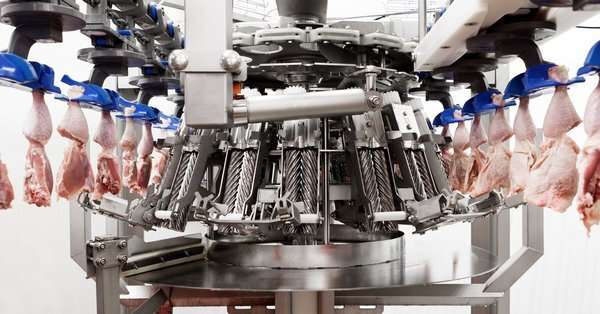
In supermarkets you can find a large variety of poultry products, all conveniently packaged in fixed-weight quantities. However, poultry processing plants face numerous challenges due to these fixed-weight batches, growing throughput requirements and small profit margins. To assist the poultry processing plant industry, TU/e-researcher Kay Peeters has developed new production control and planning strategies that reduce operational costs.
Standing in front of the supermarket shelves, you find a large variety of poultry products available to choose from, ranging from legs, to wings, filets products, or even whole chickens. Most of them conveniently packaged in fixed-weight quantities. Depending on your dinner plans or household size, you might choose the smaller 600 grams package, or the larger 1000 grams package. While enjoying the convenience of your fixed-weight package, you might not realize how vast and complex the poultry industry that produces these packages truly is.
Batches
When supermarkets order packages from poultry processing plants, they require that each package contains a certain minimum weight, while paying a fixed price per package. The batching process of poultry processing plants is responsible for making these batches of poultry products. Since no two poultry products weigh the same, it is often hard to find the right combination of products that leads to the least amount of weight over target, which is also known as giveaway. As giveaway reduces revenue, minimizing this giveaway is an important challenge for poultry processing plants.
Products such as filets are combined into batches in so-called batchers. These batchers have the option of putting an arriving product into a batch or rejecting this item and waiting for the next. Such rejections can lead to a reduction of giveaway. However, at the same time you want to make sure that the deadline of an order is met. Peeters therefore developed algorithms that make the allocation decisions for these machines. When a product with a given weight arrives at the batcher, the algorithm decides how this product should be allocated such that the deadline of an order is met, and the giveaway is minimized at the same time.
The first type of batcher he considered weighs individual items before an allocation decision is made. Consequently, making good allocation decisions is hard as the batcher does not know the weight of future products. The second type of batcher has more information and knows the weight of several products arriving in the future. Here, the question is how to use this information to minimize giveaway. Peeters implemented and tested algorithms for both types of batchers in simulation models. These tests show significant giveaway and tardiness reduction compared to the methods currently used in practice.
Already being implemented
Next, Peeters had a closer look at the planning strategies. Farmers deliver flocks of broilers to the plant daily, with each flock having a different weight histogram. Peeters’ research shows that the combination of weight histogram shape and batch weight has a strong influence on the realized giveaway. Consequently, deciding when to produce which order on which batcher is an important question. He therefore developed an algorithm, which yields the schedule with the least amount of tardiness and giveaway of all orders combined. This model and algorithm are especially relevant, as planners currently rely on Excel sheets and intuition to create production schedules, leading to unnecessarily high levels of giveaway.
Both the algorithms for controlling the batchers and the planning algorithm are highly relevant to poultry processing plants. Simulation results shows much potential, indicating that a giveaway reduction worth over a million euro could be achieved. Actually, one batcher algorithm is already being implemented. As planning algorithms needs to be able to handle a wide variety of settings—there are many ways to set up the batching process—other methods are still being developed further to make poultry packaging more efficient.