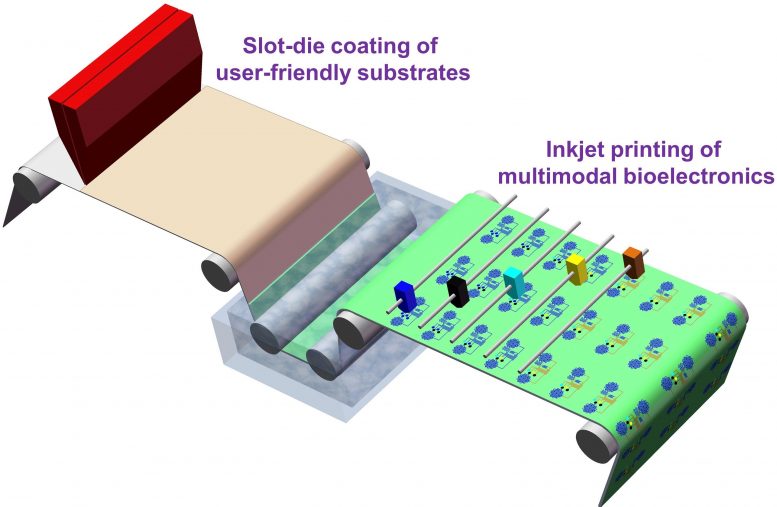
University of Missouri engineers are advancing the commercial market for wearable bioelectronics by developing a large-scale manufacturing plan for a customizable device capable of simultaneously tracking multiple vital signs such as blood pressure, heart activity and skin hydration. Credit: University of Missouri
A University of Missouri engineer received a grant from the National Science Foundation to plan for large-scale manufacturing of an on-skin, wearable bioelectronic device.
One day, a wearable, bioelectronic device could wirelessly transmit a person’s vital signs — potentially providing critical information for early detection of health issues such as COVID-19 or heart disease — to a healthcare provider, eliminating the need for an in-person visit while also saving lives.
The interest for wearable bioelectronics has grown in recent years, largely fueled by the growing demand for fitness trackers that can record workouts and monitor a person’s health — from heart rate to quality of sleep. Now, University of Missouri engineers are advancing the commercial market for wearable bioelectronics by developing a large-scale manufacturing plan for a customizable device capable of simultaneously tracking multiple vital signs such as blood pressure, heart activity and skin hydration.
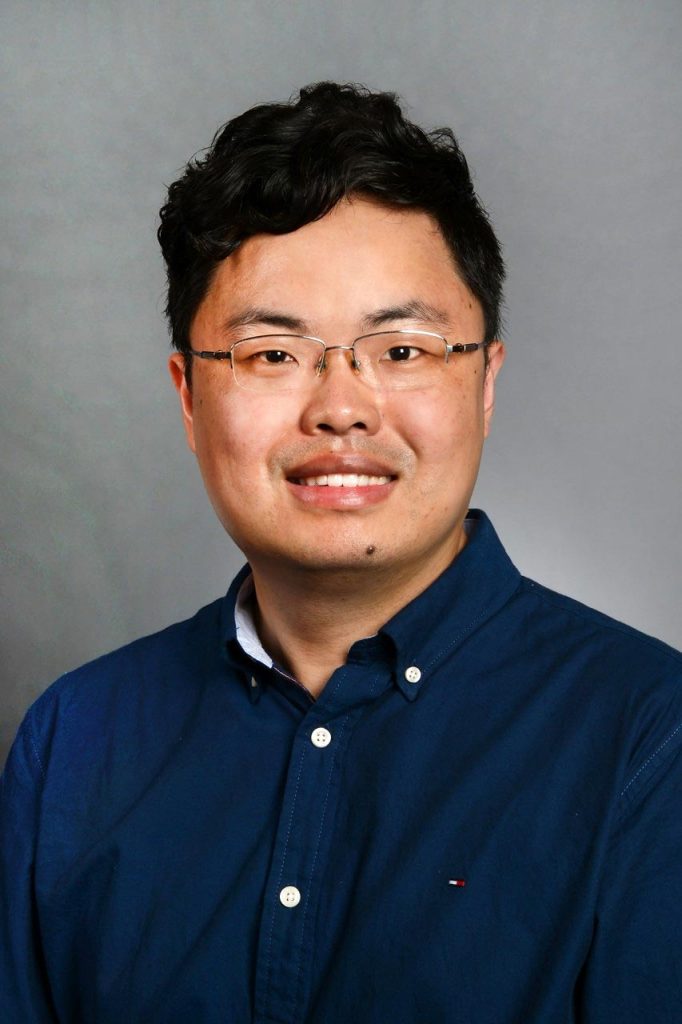
Zheng Yan. Credit: University of Missouri
“While the biosensors for these devices have already been developed, we now want to combine them to mass produce a porous patch with multiple bioelectronic components,” said Zheng Yan, an assistant professor in the College of Engineering. “The components can also be customized to fit the individual health needs of the user.”
Yan recently received a more than $500,000 grant from the National Science Foundation’s Faculty Early Career Development Program, or CAREER, to begin a plan for mass production of the low-cost device.
The grant builds on some of Yan’s previous work demonstrating a proof of concept of a small patch that works as a breathable and waterproof on-skin electronic device with passive cooling capabilities. Now, he is working to increase production of that concept device for large-scale distribution.
Yan said existing wearable devices usually consist of bioelectronics supported by a flexible, solid material — typically plastic or silicone — called a substrate. He wants to optimize the material to be soft, breathable, comfortable, lightweight and waterproof. Also, in order to mass produce the bioelectronic sensors, Yan is researching how to print them directly onto the supportive material using a method called mask-free inkjet printing.
“In the future, if we want to be able to widely implement the use of wearable biomedical devices, due to the size of production it should have a low manufacturing cost,” Yan said. “Therefore, using this grant we want to determine how to achieve continuous, scalable fabrication of such devices in an effort to keep our production costs as low as possible and transfer those cost savings to the consumer.”
The grant, “Solution based, continuous manufacturing or user friendly on skin electronics for customized health monitoring,” was awarded by the National Science Foundation (2045101).