This is an artist’s depiction of a Hyper-X research vehicle under scramjet power in free-flight following separation from its booster rocket. New research into hypersonic jets may transform space travel by making scramjet engines more reliable and efficient, leading to aircraft-like spacecraft. Credit: NASA
Wind Tunnel Study Reveals Hypersonic Jet Engine Flow Can Be Controlled Optically
Researchers at the University of Virginia are exploring the potential of hypersonic jets for space travel, using innovations in engine control and sensing techniques. The work, supported by
NASA culled a lot of useful data from the tests, as did the Air Force six years later in similar tests on the X-51 Waverider, before the prototypes careened into the ocean.
Although hypersonic proof of concept was successful, the technology was far from operational. The challenge was achieving engine control, because the tech was based on decades-old sensor approaches.
NASA’s B-52B launch aircraft cruises to a test range over the Pacific Ocean carrying the third and final X-43A vehicle, attached to a Pegasus rocket, on November 16, 2004. Credit: NASA / Carla Thomas
Breakthroughs in Hypersonic Engine Control
This month, however, brought some hope for potential successors to the X-plane series.
As part of a new NASA-funded study, University of Virginia School of Engineering and Applied Science researchers published data in the June issue of the journal Aerospace Science and Technology that showed for the first time that airflow in supersonic combusting jet engines can be controlled by an optical sensor. The finding could lead to more efficient stabilization of hypersonic jet aircraft.
In addition, the researchers achieved adaptive control of a scramjet engine, representing another first for hypersonic propulsion. Adaptive engine control systems respond to changes in dynamics to keep the system’s overall performance optimal.
“One of our national aerospace priorities since the 1960s has been to build single-stage-to-orbit aircraft that fly into space from horizontal takeoff like a traditional aircraft and land on the ground like a traditional aircraft,” said professor Christopher Goyne, director of the UVA Aerospace Research Laboratory, where the research took place.
“Currently, the most state-of-the-art craft is the 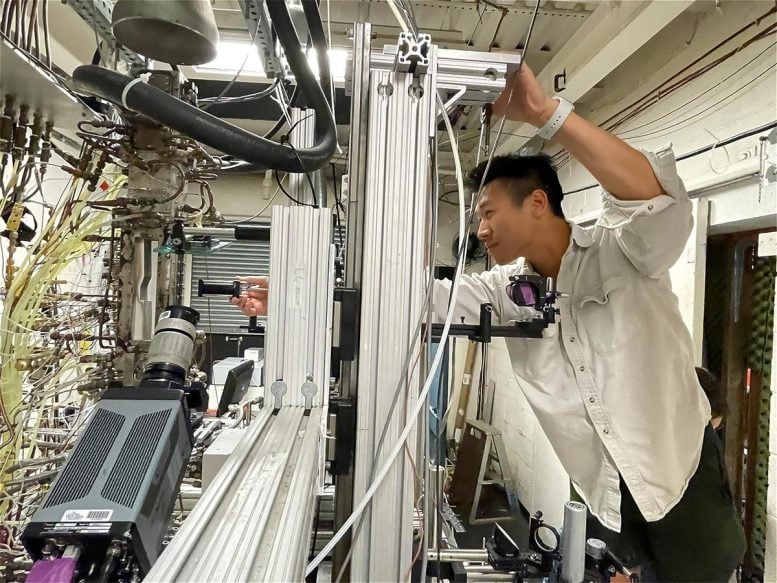
Doctoral student Max Chern takes a closer look at the wind tunnel setup where University of Virginia School of Engineering and Applied Science researchers demonstrated that control of a dual-mode scramjet engine is possible with an optical sensor. Credit: Wende Whitman, UVA Engineering
Goyne and his co-investigator, Chloe Dedic, a UVA Engineering associate professor, believe optical sensors could be a big part of the control equation.
“It seemed logical to us that if an aircraft operates at hypersonic speeds of Mach 5 and higher, that it might be preferable to embed sensors that work closer to the speed of light than the speed of sound,” Goyne said.
Additional members of the team were doctoral student Max Chern, who served as the paper’s first author, as well as former graduate student Andrew Wanchek, doctoral student Laurie Elkowitz and UVA senior scientist Robert Rockwell. The work was supported by a NASA ULI grant led by Purdue University.
Enhancing Scramjet Engine Performance
NASA has long sought to prevent something that can occur in scramjet engines called “unstart.” The term indicates a sudden change in airflow. The name derives from a specialized testing facility called a supersonic wind tunnel, where a “start” means the wind has reached the desired supersonic conditions.
UVA has several supersonic wind tunnels, including the UVA Supersonic Combustion Facility, which can simulate engine conditions for a hypersonic vehicle traveling at five times the speed of sound.
“We can run test conditions for hours, allowing us to experiment with new flow sensors and control approaches on a realistic engine geometry,” Dedic said.
Goyne explained that “scramjets,” short for supersonic combustion ramjets, build on ramjet technology that has been in common use for years.
This computational fluid dynamics image from the original Hyper-X tests shows the engine operating at Mach 7. Credit: NASA
Ramjets essentially “ram” air into the engine using the forward motion of the aircraft to generate the temperatures and pressures needed to burn fuel. They operate in a range of about Mach 3 to Mach 6. As the inlet at the front of the craft narrows, the internal air velocity slows down to subsonic speeds in a ramjet combustion engine. The plane itself, however, does not.
Scramjets are a little different, though. While they are also “air-breathing” and have the same basic setup, they need to maintain that super-fast airflow through the engine to reach hypersonic speeds.
“If something happens within the hypersonic engine, and subsonic conditions are suddenly created, it’s an unstart,” Goyne said. “Thrust will suddenly decrease, and it may be difficult at that point to restart the inlet.”
Testing a Dual-Mode Scramjet Engine
Currently, like ramjets, scramjet engines need a step-up to get them to a speed where they can intake enough oxygen to operate. That may include a ride attached to the underside of a carrier aircraft as well as a rocket boost.
The latest innovation is a dual-mode scramjet combustor, which was the type of engine the UVA-led project tested. The dual engine starts in ramjet mode at lower Mach numbers, then shifts into receiving full supersonic airflow in the combustion chamber at speeds exceeding Mach 5.
Preventing unstart as the engine makes that transition is crucial.
Christopher Goyne, professor and director of the UVA Aerospace Research Laboratory, and Chloe Dedic, associate professor. Credit: Wende Whitman, UVA Engineering
Incoming wind interacts with the inlet walls in the form of a series of shock waves known as a “shock train.” Traditionally, the leading edge of those waves, which can be destructive to the aircraft’s integrity, have been controlled by pressure sensors. The machine can adjust, for example, by relocating the position of the shock train.
But where the leading edge of the shock train resides can change quickly if flight disturbances alter mid-air dynamics. The shock train can pressurize the inlet, creating the conditions for unstart.
So, “If you are sensing at the speed of sound, yet the engine processes are moving faster than the speed of sound, you don’t have very much response time,” Goyne said.
He and his collaborators wondered if a pending unstart could be predicted by observing properties of the engine’s flame instead.
Sensing the Spectrum of a Flame
The team decided to use an optical emission spectroscopy sensor for the feedback needed to control the shock train leading edge.
No longer limited to information obtained at the engine’s walls, as pressure sensors are, the optical sensor can identify subtle changes both inside the engine and within the flow path. The tool analyzes the amount of light emitted by a source — in this case, the reacting gases within the scramjet combustor — as well as other factors, such as the flame’s location and spectral content.
“The light emitted by the flame within the engine is due to relaxation of molecular 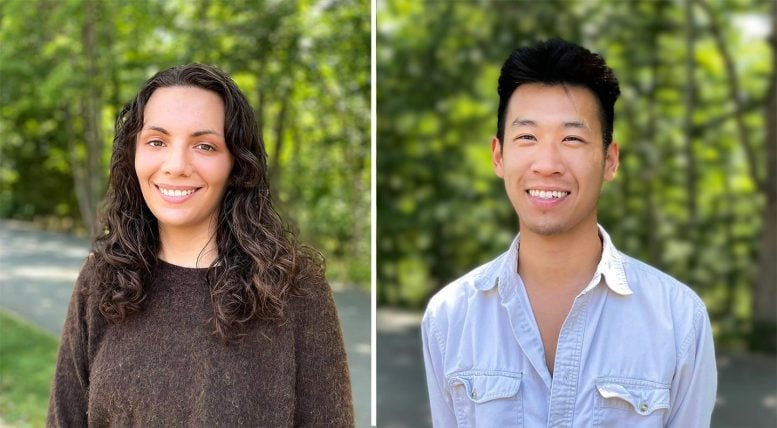
Current UVA Engineering mechanical and aerospace doctoral students Laurie Elkowitz and Max Chern were among the influential members of the team. Credit: Wende Whitman, UVA Engineering