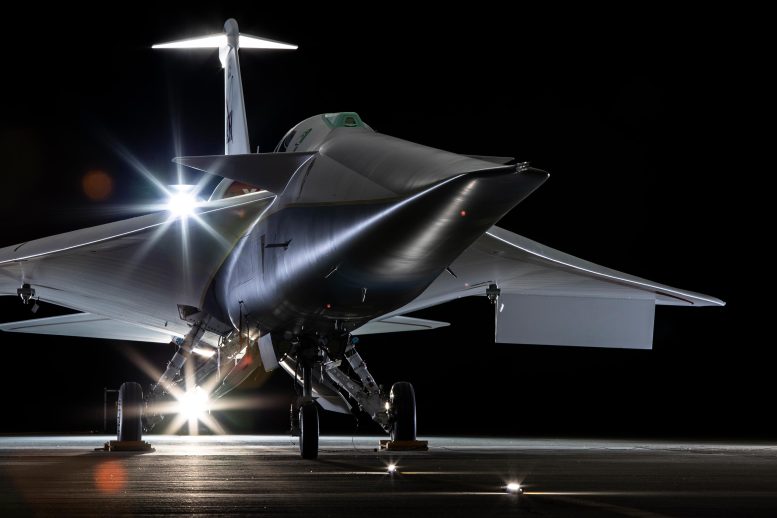
NASA’s X-59 quiet supersonic research aircraft is dramatically lit for a “glamour shot,” captured before its January 12, 2024, rollout at Lockheed Martin’s Skunk Works facility in Palmdale where the airplane was constructed. Credit: Lockheed Martin / Michael Jackson
Ground tests for
NASA recently completed a series of tests to reduce risks prior to Phase 2 of its Quesst mission, which will test the ability of the X-59 experimental aircraft to make sonic booms quieter. Credit: NASA/Steve Parcel
Preparation and Testing Phases
“We’re trying to answer questions like how many people does it take to go out and service these instruments on a daily basis, how to get the data back, how many vehicles are needed – all those sorts of things on how we operate,” said Dr. Forrest Carpenter, principal investigator for the third flight series, known as CarpetDIEM III. “We’re kind of learning how to dance now so that when we get to the big dance, we’re ready to go.”
The X-59 itself is not yet flying, so using an F-15 and an F-18 from NASA Armstrong, the CarpetDIEM III testing involved 20 supersonic passes with speeds ranging from Mach 1.15 to Mach 1.4, at altitudes ranging from 40,000 to 53,000 feet. Three of the passes involved an F-18 conducting a special inverted dive maneuver to simulate a quiet sonic boom, with one getting as quiet as 67 perceived level decibels, a measure of the perceived noisiness of the jet for an observer on the ground.
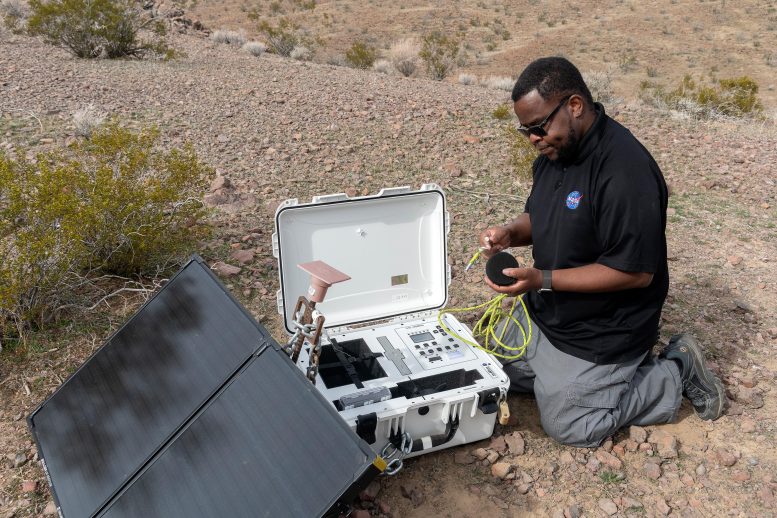
Aerospace engineer Larry Cliatt, Quesst Phase 2 sub-project manager and technical lead for the acoustic validation phase of the Quesst mission, sets up a ground recording system in the California desert. The Quesst mission recently completed testing of operations and equipment to be used in recording the sonic thumps of the X-59. The testing was the third phase of Carpet Determination in Entirety Measurements flights, called CarpetDIEM for short. An F-15 and an F-18 from NASA’s Armstrong Flight Research Center in Edwards, California, created sonic booms, both loud and soft, to verify the operations of ground recording systems spread out across 30 miles of open desert. Credit: NASA/Steve Freeman
Lowering Sonic Boom Loudness
“We expect the X-59 sonic thump to be as low as about 75 perceived loudness decibels,” said Larry Cliatt, sub-project manager for the Quesst acoustic validation phase. “That is a lot quieter than the Concorde, which was over 100 perceived loudness decibels.”
In order to measure these very quiet sonic thumps, the ground recording systems used in the CarpetDIEM flights were calibrated to measure as low as about 50 perceived loudness decibels – the equivalent to being in the room with a running refrigerator.
CarpetDIEM III also validated the use of Automatic Dependent Surveillance-Broadcast, an existing technology flown on all commercial aircraft and most private aircraft to report speed and position. This system triggers the ground recording systems to begin recording.
“We can’t have 70 different people at every single instrumentation box,” Cliatt said. “We had to find a way to automate that process.”
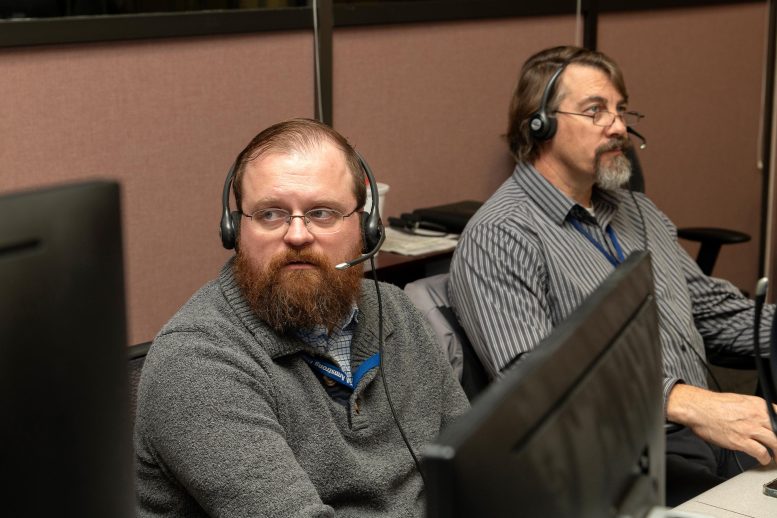
Dr. Forrest Carpenter, left, principal investigator for the third phase of CarpetDIEM, Carpet Determination in Entirety Measurements flights, monitors a test from one of the control rooms at NASA’s Armstrong Flight Research Center in Edwards, California. Next to Carpenter is Brian Strovers, chief engineer for Commercial Supersonic Technology. The third phase of CarpetDIEM tested logistics and upgraded ground recording systems in preparation for the acoustic validation phase of the Quesst mission. Credit: NASA/Steve Freeman
Durability and Efficiency
The recording systems are designed to withstand the desert elements, the extreme heat of summer, and the cold of winter, and to be resistant to damage from wildlife, such as chewing by rodents, coyotes, and foxes.
“When we get to Phase 2 of the Quesst mission, we expect to be doing these recordings of sonic thumps for up to nine months,” Cliatt said. “We need to be able to have instrumentation and operations that can facilitate such a long deployment.”
Another lesson learned – setup time for the recording stations was just under an hour, compared to the anticipated 2 1/2 hours. Given the performance of the systems, the team will assess whether they need to visit all the sites every day of Phase 2 testing.
Collaboration and Coordination
The team also learned about the coordination and documentation processes needed for such research, both with internal organizations, such as NASA Armstrong’s Environmental and Safety offices, and with outside parties including:
- The U.S. Bureau of Land Management, which gave approval to use public lands for the testing
- Law enforcement, which helped secure the test site
- The Federal Aviation Administration, which gave approval for NASA jets to fly outside the Edwards Air Force Base restricted airspace in order to conduct a portion of the CarpetDIEM tests
Looking Ahead
To prepare for Quesst Phase 2, researchers expect to conduct practice sessions in 2024, incorporating all the lessons learned and best practices from all three phases of CarpetDIEM.