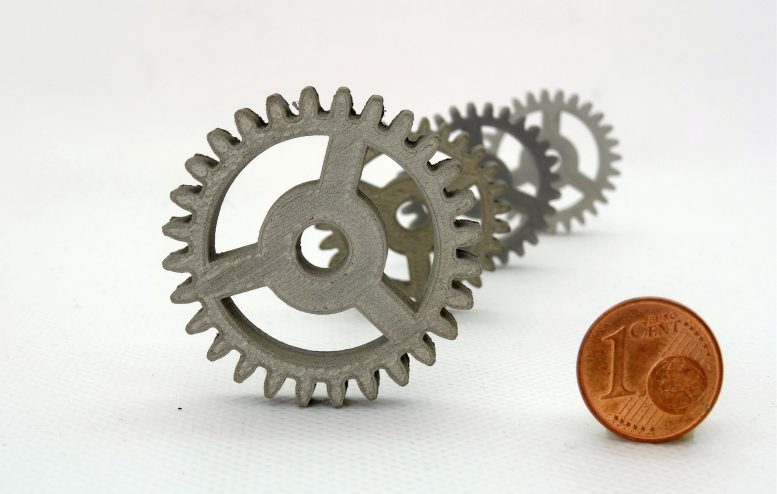
These spur gears – seen here with a euro cent coin for scale – have been produced in stainless steel to a space standard of quality using nothing more than an off-the-shelf desktop 3D printer. Credit: TIWARI Scientific Instruments
These spur gears – seen in the image above with a euro cent coin for scale – have been produced in stainless steel to a space standard of quality using nothing more than an off-the-shelf desktop 3D printer.
ESA-supported startup TIWARI Scientific Instruments in Germany has developed a technique allowing low cost 3D printing using a variety of metals and ceramics. Ordinarily producing precision parts in such high-performance materials would be costly in both time and money, but the company can instead shape them using standard 3D printing techniques.
TIWARI’s ‘Fused Filament Fabrication’ (FFF) print process uses thermoplastic filaments that are embedded with particles of the metal or ceramic the part is to be made from. Once the printing is finished, the part – known as a ‘green body’ – is put through a thermal treatment to eliminate the plastic, leaving behind a metal or ceramic item.
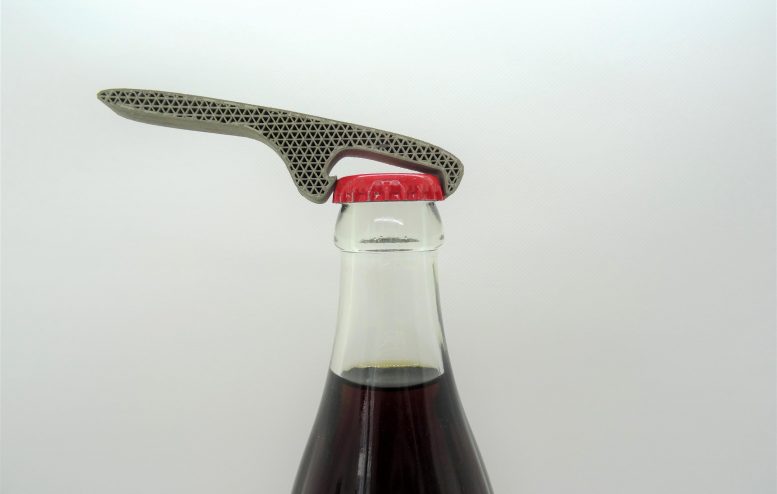
This working bottle opener has been 3D printed in stainless steel to a space standard of quality using nothing more than an off-the-shelf desktop 3D printer. Credit: TIWARI Scientific Instruments
“Once this plastic-containing body goes through this treatment then what is left behind is pure metal or ceramic,” explains ESA non-metallic materials and processes engineer Ugo Lafont. “The result is high-quality parts with very good physical properties. So this cheap, simple technique can offer us additional part manufacturing capability for space applications with an expanded pallet of materials.”
Test parts made using the FFF process in stainless steel and titanium metals, as well as aluminia ceramic and silicon carbide ceramics underwent a full-scale campaign of non-destructive and destructive testing at the Materials and Electrical Components Laboratory of ESA’s ESTEC technical center in the Netherlands, assessing their added value and suitability for space.
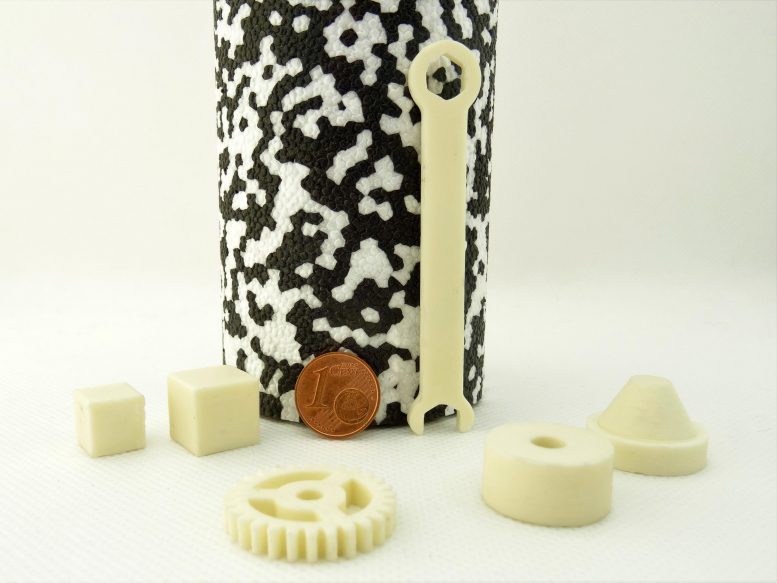
These parts – seen here with a euro cent coin for scale – have been produced in aluminia ceramic to a space standard of quality using nothing more than an off-the-shelf desktop 3D printer. Credit: TIWARI Scientific Instruments
One surprise has been that the parts possess enhanced mechanical performance compared to their conventionally made equivalents – for instance, stainless steel can be elongated to a previously unachievable 100% without breaking.
TIWARI is a startup hosted at ESA’s Business Incubation Centre Hessen & Baden-Württemberg in Germany, specializing in instruments for thermal characterization of materials as well as 3D printing of high-performance metals and ceramics.
“Desktop 3D printers have become cheaper and cheaper in recent years and there’s been a lot of interest in mixing in materials with traditional print stock,” explains company founder Siddharth Tiwari. “But our company’s particular focus has really been on understanding the process thoroughly and investigating the kind of thermal and mechanical properties we can achieve.
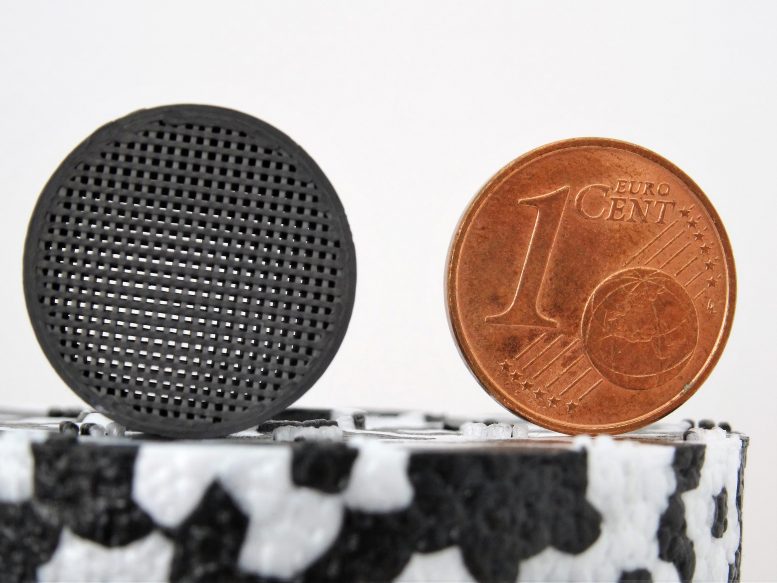
This filter – seen here with a euro cent coin for scale – has been produced in silicon carbide to a space standard of quality using nothing more than an off-the-shelf desktop 3D printer. Credit: TIWARI Scientific Instruments
“So this test campaign with ESA was part of our strategic planning from the start, to help commercialize the technology. At a time when other companies are still speculating about the properties achievable with 3D printed parts we have tested and qualified not one but four separate materials.
“This means we’ve ended up with a database no other company possesses, thanks to being able to make use of ESA resources – which otherwise would have cost many tens of thousands of euros. And the fact that our parts make the grade for space helps us in terrestrial markets too.”
The collaboration between the ESA and TIWARI on the testing and evaluation of the 3D printed parts has been facilitated by ESA’s Technology Transfer and Patent Office.
“We hope to offer an affordable solution to a market often put off by the high prices associated with additive manufacturing,” adds Siddharth Tiwari. “Our company offers one of the best price-to-performance ratio in the market, and we have launched an online estimation tool allowing customers to check how much the customized parts they require will cost.”