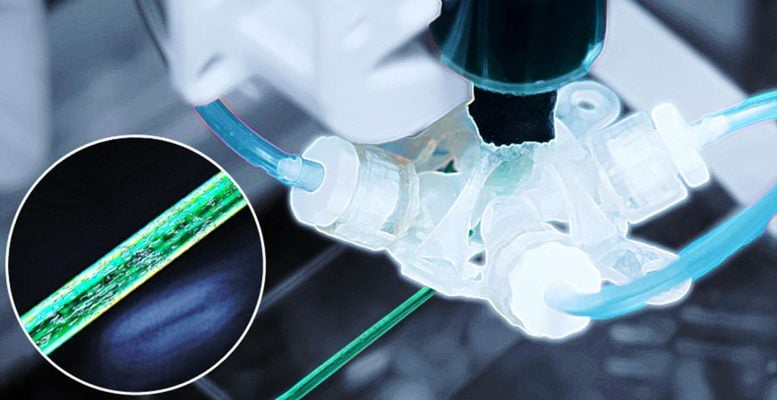
The morphing nozzle in action, 3D printing fiber-filled composite materials with on-demand control of fiber alignment for “4D printing. Credit: University of Maryland
Engineers at the University of Maryland (UMD) have created a new shape-changing or “morphing” 3D printing nozzle that was featured as a Frontispiece in the January 5th issue of the journal Advanced Materials Technologies.
The team’s morphing nozzle offers researchers new means for 3D printing “fiber-filled composites” — materials made up of short fibers that boost special properties over traditional 3D-printed parts, such as enhancing part strength or electrical conductivity. The challenge is that these properties are based on the directions or “orientations” of the short fibers, which has been difficult to control during the 3D printing process, until now.
“When 3D printing with the morphing nozzle, the power lies on their side actuators, which can be inflated like a balloon to change the shape of the nozzle, and in turn, the orientations of the fibers,” said Ryan Sochol, an assistant professor in mechanical engineering and director of the Bioinspired Advanced Manufacturing (BAM) Laboratory at UMD’s A. James Clark School of Engineering.
To demonstrate their new approach, the researchers set their sights on emerging “4D printing” applications. “4D printing refers to the relatively new concept of 3D printing objects that can reshape or transform depending on their environment,” said UMD mechanical engineering professor David Bigio, a co-author of the study. “In our work, we looked at how printed parts swelled when submerged in water, and specifically, if we could alter that swelling behavior using our morphing nozzle.”
Recent advances in 4D printing rely on materials capable of both “anisotropic” expansion, swelling more in one direction than another, as well as “isotropic” expansion, swelling identically in all directions. Unfortunately, switching between these conditions has typically required researchers to print with multiple, different materials.
“What was exciting was discovering that we could cause a single printed material to transition between anisotropic and isotropic swelling just by changing the nozzle’s shape during the 3D printing process,” said Connor Armstrong, lead author of the study. Armstrong developed the approach as part of his MS thesis research at UMD.
“Importantly, the nozzle’s ability to morph and to even up the score in terms of swelling properties is not limited to 4D printing,” said study co-author and recently graduated mechanical engineering undergraduate student Noah Todd. “Our approach could be applied for 3D printing many other composite materials to customize their elastic, thermal, magnetic or electrical properties for example.”
Interestingly, to build the morphing nozzle itself, the team actually turned to a different 3D printing technology called “PolyJet Printing.” This multi-material inkjet-based approach offered by UMD’s Terrapin Works 3D Printing Hub allowed the researchers to 3D print their nozzle with flexible materials for the inflatable side actuators and the shape-changing central channel, but then rigid materials for the outer casing and the access ports.
“The use of multi-material PolyJet 3D printing enabled us to design the nozzle with an operating power range or set of pressure magnitudes that can be reproduced in essentially any research laboratory,” said study co-author and mechanical engineering PhD candidate Abdullah Alsharhan.
In one application of this new approach, the team is exploring the use of their strategy to realize biomedical applications in which bulk printed objects could reshape in the presence of particular stimuli from the body. The team is also in discussions with several DoD laboratories to use the morphing nozzle to support the production of weapons for defense and other military systems.
“By providing researchers with an accessible way to 3D print fiber-filled composite materials with on-demand control of their fiber orientations, and thus, their ultimate performance,” Sochol said, “this work opens the door for new applications of 3D printing that harness these unique material properties and the distinctive capabilities they enable.”
Reference: “Morphing‐Nozzle 3D Printing: A 3D Printed Morphing Nozzle to Control Fiber Orientation during Composite Additive Manufacturing” by Connor D. Armstrong, Noah Todd, Abdullah T. Alsharhan, David I. Bigio and Ryan D. Sochol, 5 January 2021, Advanced Materials Technologies.DOI: 10.1002/admt.202170004