Jet packs, robot maids, and flying cars were all promises for the 21st century. We got mechanized, autonomous vacuum cleaners instead. Now a team of Penn State researchers are exploring the requirements for electric vertical takeoff and landing (eVTOL) vehicles and designing and testing potential battery power sources.
“I think flying cars have the potential to eliminate a lot of time and increase productivity and open the sky corridors to transportation,” said Chao-Yang Wang, holder of the William E. Diefender Chair of Mechanical Engineering and director of the Electrochemical Engine Center, Penn State. “But electric vertical takeoff and landing vehicles are very challenging technology for the batteries.”
The researchers defined the technical requirements for flying car batteries and report on a prototype battery on June 7, 2021, in Joule.
“Batteries for flying cars need very high energy density so that you can stay in the air,” said Wang. “And they also need very high power during take-off and landing. It requires a lot of power to go vertically up and down.”
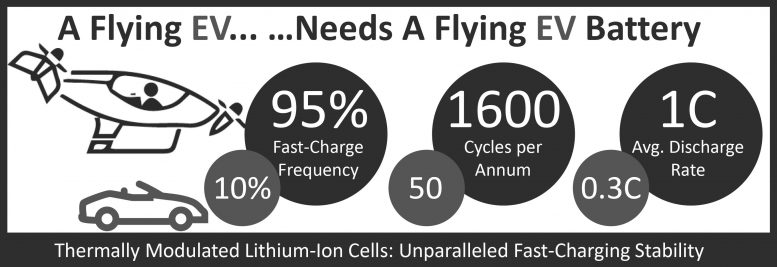
The automotive electric vehicle revolution is paving the way for urban air mobility, but people must not be naive in thinking that electric vehicle batteries will suffice for electric flight. The fast-charging requirements, 30x increase in energy throughput, and 3x power requirements demand a new generation of battery. Credit: Eric Rountree, EC Power
Wang notes that the batteries will also need to be rapidly recharged so that there could be high revenue during rush hours. He sees these vehicles having frequent take-offs and landings and recharging quickly and often.
“Commercially, I would expect these vehicles to make 15 trips, twice a day during rush hour to justify the cost of the vehicles,” said Wang. “The first use will probably be from a city to an airport carrying three to four people about 50 miles.”
Weight is also a consideration for these batteries as the vehicle will have to lift and land the batteries. Once the eVTOL takes off, on short trips the average speed would be 100 miles per hour and long trips would average 200 miles per hour, according to Wang.
The researchers experimentally tested two energy-dense lithium-ion batteries that can recharge with enough energy for a 50-mile eVTOL trip in five to ten minutes. These batteries could sustain more than 2,000 fast-charges over their lifetime.
Wang and his team used technology they have been working on for electric vehicle batteries. The key is to heat the battery to allow rapid charging without the formation of lithium spikes that damage the battery and are dangerous. It turns out that heating the battery also allows rapid discharge of the energy held in the battery to allow for take offs and landings.
The researchers heat the batteries by incorporating a nickel foil that brings the battery rapidly to 140 degrees Fahrenheit.
“Under normal circumstances, the three attributes necessary for an eVTOL battery work against each other,” said Wang. “High energy density reduces fast charging and fast charging usually reduces the number of possible recharge cycles. But we are able to do all three in a single battery.”
One entirely unique aspect of flying cars is that the batteries must always retain some charge. Unlike cellphone batteries, for example, that work best if fully discharged and recharged, a flying car battery can never be allowed to completely discharge in the air because power is needed to stay in the air and to land. There always needs to be a margin of safety in a flying car battery.
When a battery is empty, internal resistance to charging is low, but the higher the remaining charge, the more difficult it is to push more energy into the battery. Typically, recharging slows as the battery fills. However, by heating the battery, recharging can remain in the five- to ten-minute range.
“I hope that the work we have done in this paper will give people a solid idea that we don’t need another 20 years to finally get these vehicles,” said Wang. “I believe we have demonstrated that the eVTOL is commercially viable.”
Reference: “Challenges and key requirements of batteries for electric vertical takeoff and landing aircraft” by Xiao-Guang Yang, Teng Liu, Shanhai Ge, Eric Rountree and Chao-Yang Wang, 7 June 2021, Joule.DOI: 10.1016/j.joule.2021.05.001
Also working on this project were Xiao-Guang Yang and Shanhai Ge, both assistant research professors in mechanical engineering, and Teng Liu, doctoral student in mechanical engineering, all at Penn State; and Eric Roundtree, EC Power, State College, Pennsylvania.
The U.S. Department of Energy’s Office of Energy Efficiency and Renewable Energy, the U.S. Air Force Small Business Technology Transfer program and the William E. Diefenderfer Endowment funded this research.