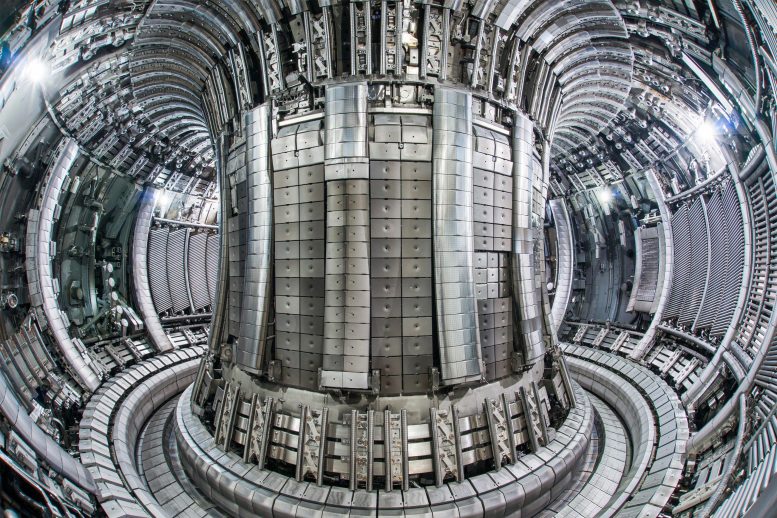
Nuclear fusion energy could be a pivotal sustainable energy source to complement renewables. The world’s largest fusion experiment, ITER, is being built in France. Credit: ITER Organization
Major milestone in European and Japanese contributions to ITER fusion energy project.
The ITER fusion energy project marks a significant milestone with the completion of 19 toroidal field coils, crucial for magnetic confinement in fusion energy. Developed over two decades through a multinational effort, these components signify a step forward in producing a clean, abundant energy source. This project demonstrates exceptional international collaboration and technological innovation, involving over 30 countries and numerous high-tech companies.
After two decades of design, production, fabrication, and assembly on three continents, the historic, multinational ITER fusion energy project celebrates the completion and delivery of its massive toroidal field coils from Japan and Europe.
Masahito Moriyama, Japan’s Minister of Education, Culture, Sports, Science and Technology, and Gilberto Pichetto Fratin, Italy’s Minister of Environment and Energy Security, will attend the ceremony with officials from other ITER members.
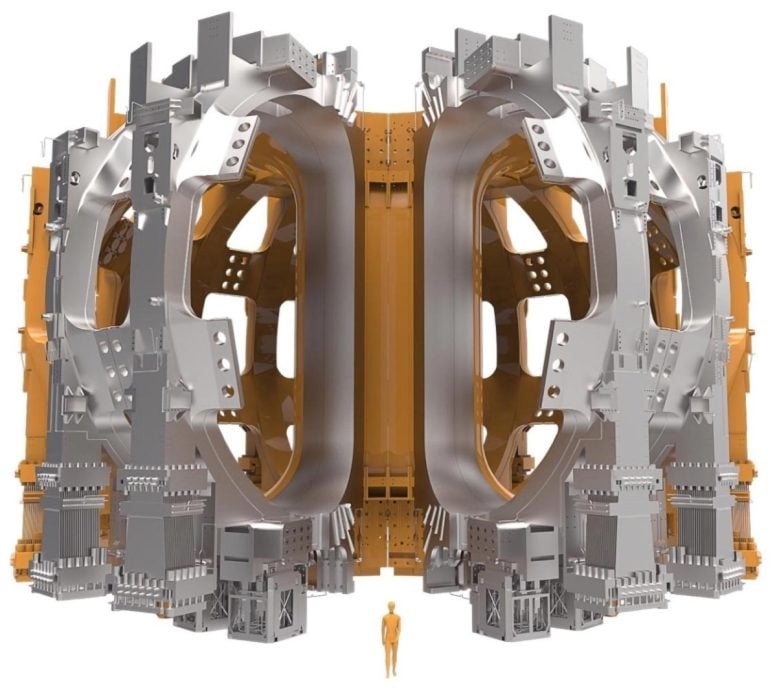
How the toroidal field coils fit around the tokamak vacuum vessel (including human scale). Credit: ITER
How does fusion work?
- A small amount of deuterium and tritium (hydrogen) gas is injected into a large, donut-shaped vacuum chamber, called a tokamak.
- The hydrogen is heated until it becomes an ionized After two decades of design, production, fabrication, and assembly on three continents, the historic, multinational ITER fusion energy project celebrates the completion and delivery of its massive toroidal field coils from Japan and Europe. Credit: Fusion for Energy
Engineering the Future of Energy
The plasma will be heated to 150 million degrees, 10 times hotter than the core of the sun. At this temperature, the velocity of the light atomic nuclei is high enough for them to collide and fuse. To shape, confine, and control this extremely hot plasma, the ITER tokamak must generate an invisible magnetic cage, precisely conformed to the shape of the metal vacuum vessel.
ITER uses niobium-tin and niobium-titanium as the material for its giant coils. When energized with electricity, the coils become electromagnets. When cooled with liquid helium to -269 degrees Celsius (4 Kelvin), they become superconducting.
The Core Components of ITER
To create the precise magnetic fields required, ITER employs three different arrays of magnets. The eighteen D-shaped toroidal field magnets confine the plasma inside the vessel. The poloidal field magnets, a stacked set of six rings that circle the tokamak horizontally, control the position and shape of the plasma.
At the center of the tokamak, the cylindrical central solenoid uses a pulse of energy to generate a powerful current in the plasma. At 15 million amperes, ITER’s plasma current will be far more powerful than anything possible in current or previous tokamaks.
Ten coils were manufactured in Europe, under the auspices of ITER’s European Domestic Agency, Fusion for Energy (F4E). Eight coils plus one spare were made in Japan, managed by ITER Japan, part of the National Institutes for Quantum Science and Technology (QST).
Each completed coil is huge: 17 meters tall and 9 meters across, and weighing about 360 tons.
The toroidal field coils will operate together, in effect, as a single magnet: the most powerful magnet ever made.
They will generate a total magnetic energy of 41 gigajoules. ITER’s magnetic field will be about 250,000 times stronger than that of the Earth.
Making the Toroidal Field Coils
The fabrication process began with production of niobium-tin strand. More than 87,000 kilometers of thin wire was needed to create 19 toroidal field coils. This strand was produced in China, Europe, Japan, Korea, Russia, and the United States.
Hundreds of niobium-tin strands were wound with copper strands into a rope-like cluster, and inserted into a steel jacket, with a central channel to accommodate the forced flow of liquid helium.
The result – a “cable-in-conduit,” or simply “conductor” – forms the core element of the coils. This conductor material was shipped to Japan and Europe to begin the fabrication process.
The actual fabrication was even more challenging. To start, about 750 meters of the conductor was bent into a double-spiral trajectory and heat-treated at 650 degrees Celsius. It was then fitted precisely into a D-shaped “radial plate,” a stainless steel structure with grooves on both sides into which the conductor nestles.
The conductor was wrapped and insulated using glass and Kapton tape. Cover plates were fitted and laser-welded. This created a “double pancake,” a huge but delicate sub-component made of two layers of conductor. The whole double pancake was then wrapped again in insulating tape and injected with resin to add structural strength, using vacuum to remove any air pockets.
In the next stage, seven double pancakes were stacked to make a “winding pack,” forming the core of the eventual magnet. Each double pancake was joined to the next for electrical continuity. The overall winding pack was insulated, heat treated, and again injected with resin.
Lastly, the winding pack was inserted into a massive, fit-for-purpose stainless steel case, weighing about 200 tonnes, strong enough to resist the immense forces that will be generated during ITER operation.
More than 40 companies and more than 000 expert technicians were involved in the creation of the toroidal field (TF) coils. Some of the key European companies include:
- ASG Superconductors manufactured 70 TF double pancakes and 10 winding packs.
- CNIM manufactured 35 TF radial plates.
- SIMIC manufactured 35 TF radial plates and completed 10 TF coils,
- Iberdrola coordinated manufacturing of 10 TF coil winding packs.
- Elytt Energy manufactured the tooling for the 70 TF double pancakes.
- BNG completed the cold test, at 80 Kelvin, of 10 TF winding packs.
Japan was responsible for fabricating all 19 of the TF coil cases, in a collaboration between Mitsubishi Heavy Industries, Toshiba Energy Systems, and Hyundai Heavy Industries. In addition, the key companies involved in the fabrication of Japan’s TF coils include:
- Mitsubishi Electric Corporation manufactured 5 TF winding packs.
- Arisawa Manufacturing manufactured all insulation tapes.
- Mitsubishi Heavy Industries completed 5 TF Coils.
- Toshiba Energy Systems completed 4 TF Coils.
“The completion and delivery of the 19 ITER toroidal field coils is a monumental achievement,” said Pietro Barabaschi, ITER Director-General. “We congratulate the Member governments, the ITER Domestic Agencies, the companies involved, and the many individuals who dedicated countless hours to this remarkable endeavor.”
Source: SciTechDaily