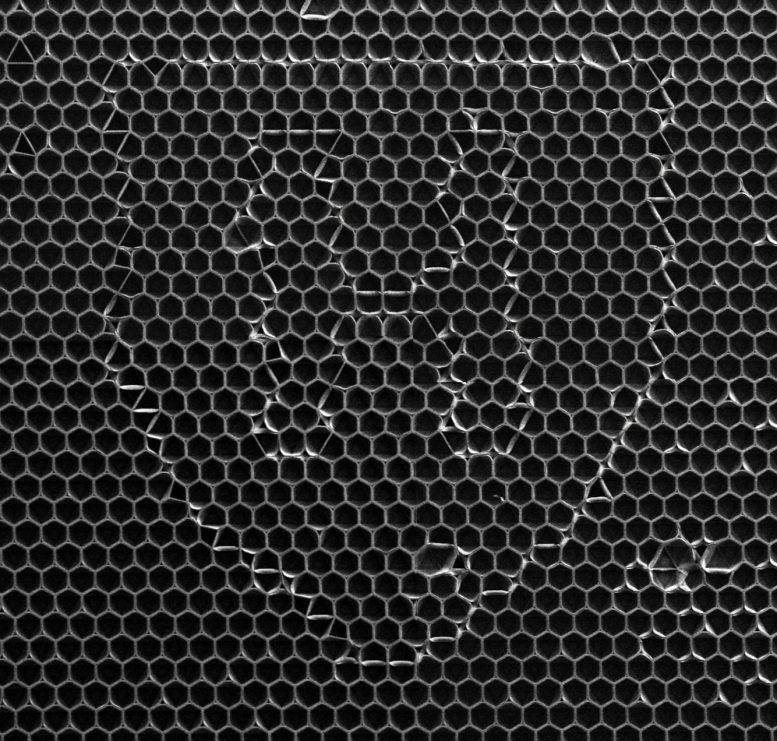
Researchers encoded patterns and designs into the material by making tiny, invisible tweaks to the geometry of the triangular lattice. Credit: Image courtesy of Shucong Li/Bolei Deng/Harvard SEAS
Reconfigurable materials can do amazing things. Flat sheets transform into a face. An extruded cube transforms into dozens of different shapes. But there’s one thing a reconfigurable material has yet to be able to change: its underlying topology. A reconfigurable material with 100 cells will always have 100 cells, even if those cells are stretched or squashed.
Now, researchers from the Harvard John A. Paulson School of Engineering and Applied Sciences (SEAS) have developed a method to change a cellular material’s fundamental topology at the microscale. The research is published in Nature.
“Creating cellular structures capable of dynamically changing their topology will open new opportunities in developing active materials with information encryption, selective particle trapping, as well as tunable mechanical, chemical and acoustic properties,” said Joanna Aizenberg, the Amy Smith Berylson Professor of Materials Science at SEAS and Professor of Chemistry & Chemical Biology and senior author of the paper.
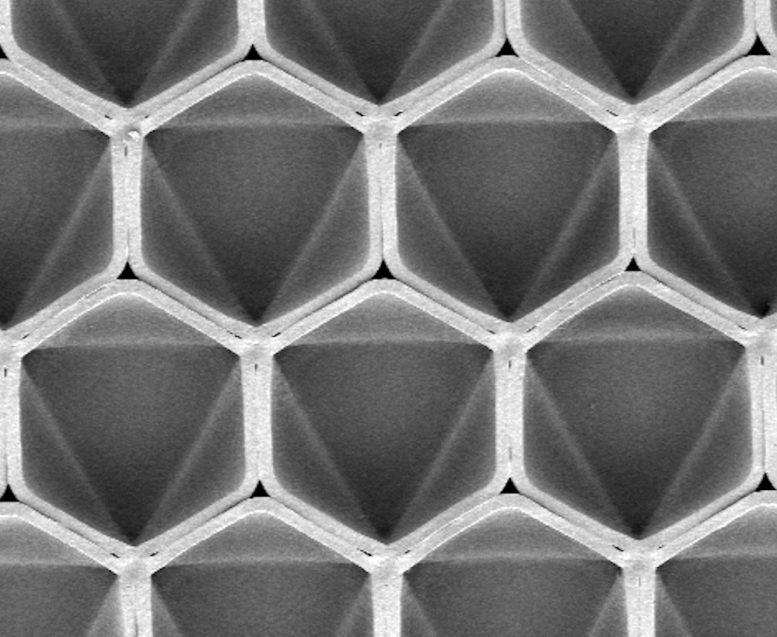
Researchers developed a method to change a cellular material’s fundamental topology at the microscale, paving the way for active materials with tunable mechanical, chemical and acoustic properties. Credit: Images courtesy of Shucong Li/Bolei Deng/Harvard SEAS
The researchers harnessed the same physics that clumps our hair together when it gets wet — capillary force. Capillary force works well on soft, compliant material, like our hair, but struggles with stiff cellular structures that require the bending, stretching or folding of walls, especially around strong, connected nodes. Capillary force is also temporary, with materials tending to return to their original configuration after drying.
In order to develop a long-lasting yet reversible method to transform the topology of stiff cellular microstructures, the researchers developed a two-tiered dynamic strategy. They began with a stiff, polymeric cellular microstructure with a triangular lattice topology, and exposed it to droplets of a volatile solvent chosen to swell and soften the polymer at the molecular scale. This made the material temporarily more flexible and in this flexible state, the capillary forces imposed by the evaporating liquid drew the edges of the triangles together, changing their connections with one another and transforming them into hexagons. Then, as the solvent rapidly evaporated, the material dried and was trapped in its new configuration, regaining its stiffness. The whole process took a matter of seconds.
“When you think about applications, it’s really important not to lose a material’s mechanical properties after the transformation process,” said Shucong Li, a graduate student in the Aizenberg Lab and co-first author of the paper. “Here, we showed that we can start with a stiff material and end with a stiff material through the process of temporarily softening it at the reconfiguration stage.”
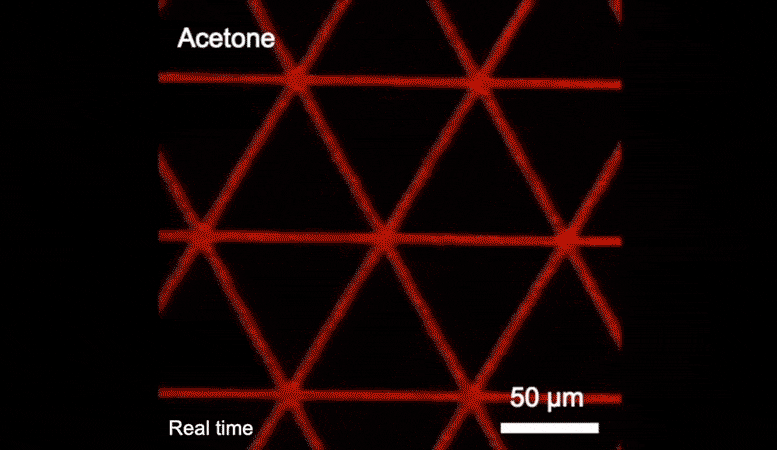
Video of the assembly of the microstructures. The triangle lattice is exposed to a liquid which swells and softens the polymer. In this flexible state, the capillary forces imposed by the evaporating liquid drew the edges of the triangles together, changing their connections with one another and transforming them into hexagons. Credit: Video courtesy of Shucong Li/Bolei Deng/Harvard SEAS
The new topology of the material is so durable it can withstand heat or be submerged in some liquids for days without disassembling. Its robustness actually posed a problem for the researchers who had hoped to make the transformation reversible.
To return to the original topology, the researchers developed a technique that combines two liquids. The first temporarily swells the lattice, which peels apart the adhered walls of the hexagons and allows the lattice to return to its original triangular structure. The second, less volatile liquid delays the emergence of capillary forces until the first liquid has evaporated and the material has regained its stiffness. In this way, the structures can be assembled and disassembled repeatedly and trapped in any in-between configuration.
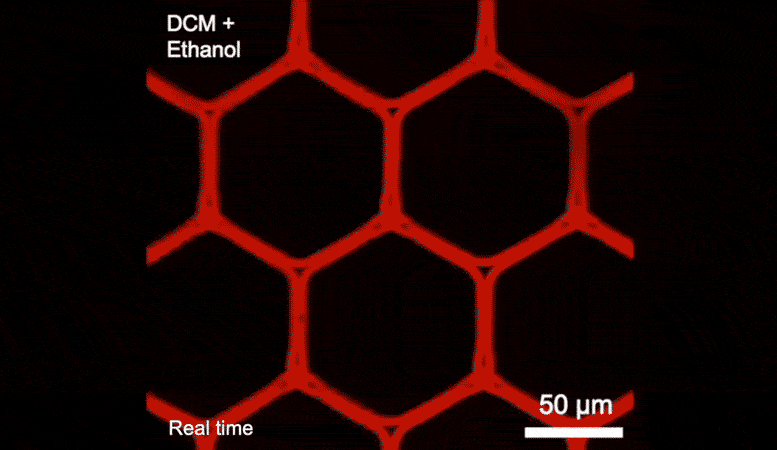
Video of the disassembly of the microstructures. The first temporarily swells the lattice, which peels apart the adhered walls. The second, less volatile liquid delays the emergence of capillary forces until the first liquid has evaporated and the material has regained its stiffness. Credit: Video courtesy of Shucong Li/Bolei Deng/Harvard SEAS
“In order to extend our approach to arbitrary lattices, it was important to develop a generalized theoretical model that connects cellular geometries, material stiffness and capillary forces,” said Bolei Deng, co-first author of the paper and graduate student in the lab of Katia Bertoldi, the William and Ami Kuan Danoff Professor of Applied Mechanics at SEAS.
Guided by this model, the researchers demonstrated programmed reversible topological transformations of various lattice geometries and responsive materials, including turning a lattice of circles into squares.
The researchers explored various applications for the study. For example, the team encoded patterns and designs into the material by making tiny, invisible tweaks to the geometry of the triangular lattice.
“You can imagine this being used for information encryption in the future, because you can’t see the pattern in the material when it’s in its unassembled state,” said Li.
The researchers also demonstrated highly local transformation, assembling and disassembling regions of the lattice with a tiny drop of liquid. This method could be used to tune the friction and wetting properties of a material, change its acoustic properties and mechanical resilience, and even trap particles and gas bubbles.
“Our strategy could be applied to a range of applications,” said Bertoldi, who is also a co-author of the paper. “We can apply this method to different materials, including responsive materials, different geometries and different scales, even the nanoscale where topology plays a key role in designing tunable photonic meta-surfaces. The design space for this is huge.”
Reference: “Liquid-induced topological transformations of cellular microstructures” by Shucong Li, Bolei Deng, Alison Grinthal, Alyssha Schneider-Yamamura, Jinliang Kang, Reese S. Martens, Cathy T. Zhang, Jian Li, Siqin Yu, Katia Bertoldi and Joanna Aizenberg, 14 April 2021, Nature.DOI: 10.1038/s41586-021-03404-7
This research was co-authored by Alison Grinthal, Alyssha Schneider-Yamamura, Jinliang Kang, Reese S. Martens, Cathy T. Zhang, Jian Li, and Siqin Yu.
It was supported by the National Science Foundation through the Designing Materials to Revolutionize and Engineer our Future (DMREF) program under award no. DMR-1922321, the Harvard University Materials Research Science and Engineering Center (MRSEC) under award no. DMR-18 2011754, and by the US Department of Energy (DOE), Office of Science, Basic Energy Sciences (BES) under award number DE-SC0005247.