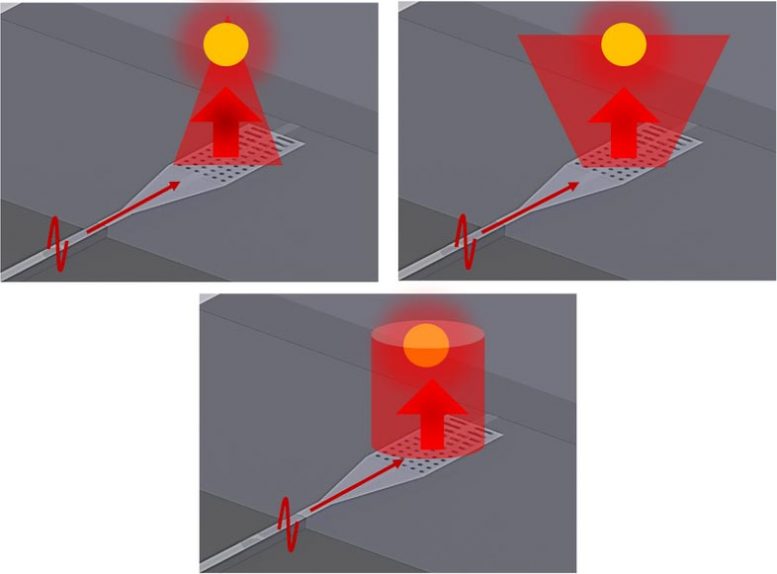
Schematic of three different nano flashlights for the generation of (left to right) focused, wide-spanning, and collimated light beams. Each flashlight could have different applications. Credit: Robin Singh
Design of miniature optical systems could lead to future cell phones that can detect viruses and more.
In work that could someday turn cell phones into sensors capable of detecting viruses and other minuscule objects, MIT researchers have built a powerful nanoscale flashlight on a chip.
Their approach to designing the tiny light beam on a chip could also be used to create a variety of other nano flashlights with different beam characteristics for different applications. Think of a wide spotlight versus a beam of light focused on a single point.
For many decades, scientists have used light to identify a material by observing how that light interacts with the material. They do so by essentially shining a beam of light on the material, then analyzing that light after it passes through the material. Because all materials interact with light differently, an analysis of the light that passes through the material provides a kind of “fingerprint” for that material. Imagine doing this for several colors — i.e., several wavelengths of light — and capturing the interaction of light with the material for each color. That would lead to a fingerprint that is even more detailed.
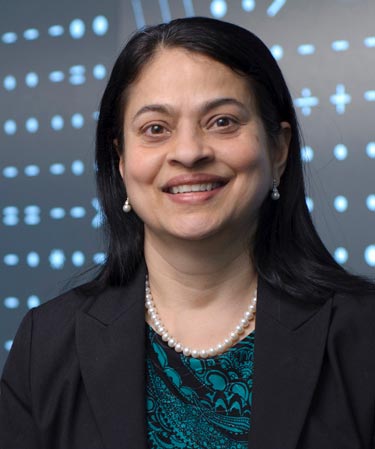
Anu Agarwal is one of the lead researchers involved in the development of a nano flashlight. Credit: Photo courtesy of Anu Agarwal
Most instruments for doing this, known as spectrometers, are relatively large. Making them much smaller would have a number of advantages. For example, they could be portable and have additional applications (imagine a futuristic cell phone loaded with a self-contained sensor for a specific gas). However, while researchers have made great strides toward miniaturizing the sensor for detecting and analyzing the light that has passed through a given material, a miniaturized and appropriately shaped light beam—or flashlight—remains a challenge. Today that light beam is most often provided by macroscale equipment like a laser system that is not built into the chip itself as the sensors are.
Complete sensor
Enter the MIT work. In two recent papers in Nature Scientific Reports, researchers describe not only their approach for designing on-chip flashlights with a variety of beam characteristics, they also report building and successfully testing a prototype. Importantly, they created the device using existing fabrication technologies familiar to the microelectronics industry, so they are confident that the approach could be deployable at a mass scale with the lower cost that implies.
Overall, this could enable industry to create a complete sensor on a chip with both light source and detector. As a result, the work represents a significant advance in the use of silicon photonics for the manipulation of light waves on microchips for sensor applications.
“Silicon photonics has so much potential to improve and miniaturize the existing bench-scale biosensing schemes. We just need smarter design strategies to tap its full potential. This work shows one such approach,” says PhD candidate Robin Singh SM ’18, who is lead author of both papers.
“This work is significant, and represents a new paradigm of photonic device design, enabling enhancements in the manipulation of optical beams,” says Dawn Tan, an associate professor at the Singapore University of Technology and Design who was not involved in the research.
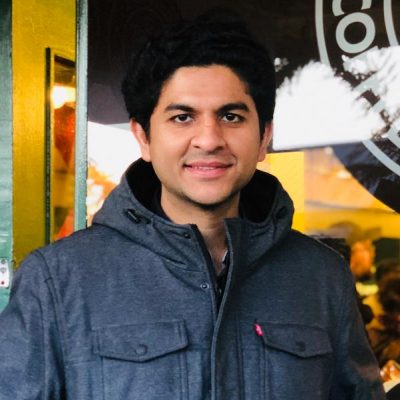
Robin Singh is one of the lead researchers involved in the development of a nano flashlight. Credit: Photo courtesy of Robin Singh
The senior coauthors on the first paper are Anuradha “Anu” Murthy Agarwal, a principal research scientist in MIT’s Materials Research Laboratory, Microphotonics Center, and Initiative for Knowledge and Innovation in Manufacturing; and Brian W. Anthony, a principal research scientist in MIT’s Department of Mechanical Engineering. Singh’s coauthors on the second paper are Agarwal; Anthony; Yuqi Nie, now at Princeton University; and Mingye Gao, a graduate student in MIT’s Department of Electrical Engineering and Computer Science.
How they did it
Singh and colleagues created their overall design using multiple computer modeling tools. These included conventional approaches based on the physics involved in the propagation and manipulation of light, and more cutting-edge machine-learning techniques in which the computer is taught to predict potential solutions using huge amounts of data. “If we show the computer many examples of nano flashlights, it can learn how to make better flashlights,” says Anthony. Ultimately, “we can then tell the computer the pattern of light that we want, and it will tell us what the design of the flashlight needs to be.”
All of these modeling tools have advantages and disadvantages; together they resulted in a final, optimal design that can be adapted to create flashlights with different kinds of light beams.
The researchers went on to use that design to create a specific flashlight with a collimated beam, or one in which the rays of light are perfectly parallel to each other. Collimated beams are key to some types of sensors. The overall flashlight that the researchers made involved some 500 rectangular nanoscale structures of different dimensions that the team’s modeling predicted would enable a collimated beam. Nanostructures of different dimensions would lead to different kinds of beams that in turn are key to other applications.
The tiny flashlight with a collimated beam worked. Not only that, it provided a beam that was five times more powerful than is possible with conventional structures. That’s partly because “being able to control the light better means that less is scattered and lost,” says Agarwal.
Singh describes the excitement he felt upon creating that first flashlight. “It was great to see through a microscope what I had designed on a computer. Then we tested it, and it worked!”
References:
“Inverse design of photonic meta-structure for beam collimation in on-chip sensing” by Robin Singh, Yuqi Nie, Mingye Gao, Anuradha Murthy Agarwal and Brian W. Anthony, 5 March 2021, Scientific Reports.DOI: 10.1038/s41598-021-84841-2
“Design of optical meta-structures with applications to beam engineering using deep learning” by Robin Singh, Anu Agarwal and Brian W. Anthony, 16 November 2020, Scientific Reports.DOI: 10.1038/s41598-020-76225-9
This research was supported, in part, by the MIT Skoltech Initiative.
Additional MIT facilities and departments that made this work possible are the Department of Materials Science and Engineering, the Materials Research Laboratory, the Institute for Medical Engineering and Science, and MIT.nano.