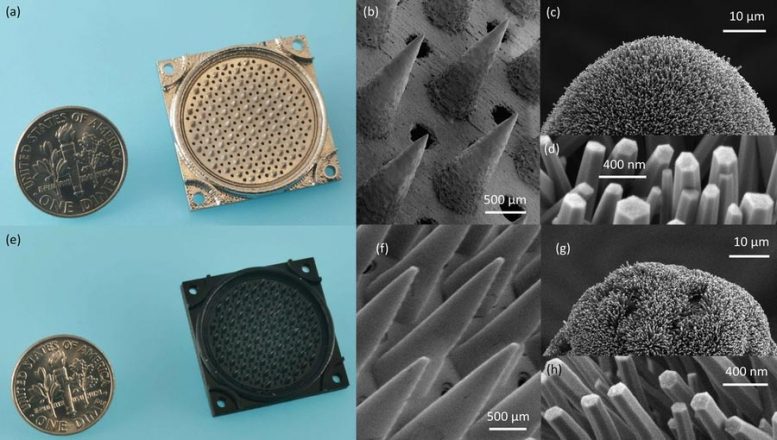
Nanosatellite thrusters that emit a stream of pure ions are the first of their kind to be entirely additively manufactured, using a combination of 3D printing and hydrothermal growth of zinc oxide nanowires. A stainless steel version (top) works better overall but is much more expensive to produce. MIT researchers found that a polymer version (bottom) yields comparable performance at a lower cost. Credit: Velásquez-García Group
Study is first demonstration of a fully 3D-printed thruster using pure ion emission for propulsion.
A 3D-printed thruster that emits a stream of pure ions could be a low-cost, extremely efficient propulsion source for miniature satellites.
The nanosatellite thruster created by MIT researchers is the first of its kind to be entirely additively manufactured, using a combination of 3D printing and hydrothermal growth of zinc oxide nanowires. It is also the first thruster of this type to produce pure ions from the ionic liquids used to generate propulsion.
The pure ions make the thruster more efficient than similar state-of-the-art devices, giving it more thrust per unit flow of propellant, says Luis Fernando Velásquez-García, principal research scientist at MIT’s Microsystems Technology Laboratories (MTL).
The thrust provided by the device, which is about the size of a dime, is minuscule. The force can be measured on the scale of a few tens of micronewtons, a thrust about equal to half the weight of one of the sesame seeds in a hamburger bun. But in the frictionless environment of orbit, a CubeSat or similarly small satellite could use these tiny thrusts to accelerate or maneuver with fine control.
Velásquez-García says additive manufacturing’s advantages offer new low-cost possibilities for powering satellites. “If you want to be serious about developing high-performance hardware for space, you really need to look into optimizing the shapes, the materials, everything that composes these systems. 3D printing can help with all of these things,” he says.
Velásquez-García and MTL postdoc Dulce Viridiana Melo Máximo describe the thruster in the December 2020 issue of the journal Additive Manufacturing. The work was sponsored by the MIT–Tecnológico de Monterrey Program in Nanoscience and Nanotechnology and the MIT Portugal program.
Electrospraying pure ions
The miniaturized thruster operates electrohydrodynamically, producing a fine spray of accelerated, charged particles that are emitted to produce a propulsive force. The particles come from a sort of liquid salt called ionic liquid.
In the MIT design, a 3D-printed body holds a reservoir of ionic liquid along with a miniature forest of emitter cones coated with zinc oxide nanowires hydrothermally grown on the cone surfaces. The nanowires act as wicks to transport the liquid from the reservoir to the emitter tips. By applying a voltage between the emitters and a 3D-printed extractor electrode, charged particles are ejected from the emitter tips. The researchers experimented with printing the emitters in a type of stainless steel as well as a polymer resin.
The researchers were able to detect the pure ion jet using a technique called mass spectrometry, which can identify the composition of particles based on their molecular mass. Typically, an electrospray produced from ionic liquids would contain ions plus other species made of ions mixed with neutral molecules.
The pure ion jet was a surprise, and the research team still isn’t entirely sure how it was produced, although Velásquez-García and his colleagues think the zinc oxide nanowires “are the secret sauce,” he says. “We believe it has something to do with the way the charge is injected and the way the fluid interacts with the wire material as it transports the fluid to the emission sites.”
Producing a jet of pure ions means that the thruster can utilize more efficiently the propellant on board, and propellant efficiency is key for objects in orbit because refueling satellites is rarely an option, he explains. “The hardware that you put into space, you want to get many, many years of use out of that, so I think it’s a good strategy to do it efficiently.”
Advantages of additive manufacturing
Electrospray designs can have many applications beyond space, says Velásquez-García. The technique “can emit not just ions, but also things like nanofibers and droplets. You could use the fibers to make filters, or electrodes for energy storage, or use the droplets to purify seawater by removing brine. You could also use electrospray designs in a combustor, to atomize fuel into very small and fine droplets.”
The nanosatellite thruster is a good example how additive manufacturing can produce devices that are “personalized, customized and made from finely featured, complex multi-material structures,” he adds. Instead of using expensive laser machining or clean-room technologies for specialized industrial manufacturing, he and his colleagues made the thruster mostly on commercial printers using instructions that can be distributed widely.
And since the techniques are relatively inexpensive, fast, and easy to use, Velásquez-García says designs can be “exquisitely iterated” to improve features and explore surprising effects, such as the pure ion emission in the case of the new thruster.
The advantages of 3D printing microsystems include lower costs and shorter times for prototyping and development, along with the ease of assembling multimaterial structures, says Tomasz Grzebyk, a microsystems professor at Wroclaw University of Science and Technology, who was not involved with the study.
“All these advantages can be seen also in the ion thrusters developed at MIT,” Grzebyk says. “And what more, since there has been a great progress in 3D printing in last few years, the parameters of devices fabricated using this method are becoming similar to these obtained by much more complex, expensive and restricted to specialized laboratories microengineering techniques.”
“3D printing technology is also constantly improving, potentially making it possible to implement in the near future even better systems that have smaller features and are made of better materials,” he says. “We are on track to producing the best possible hardware that a lot more people can afford.”
Reference: “Additively manufactured electrohydrodynamic ionic liquid pure-ion sources for nanosatellite propulsion” by Dulce Viridiana Melo Máximo and Luis Fernando Velásquez-García, 21 November 2020, Additive Manufacturing.DOI: 10.1016/j.addma.2020.101719