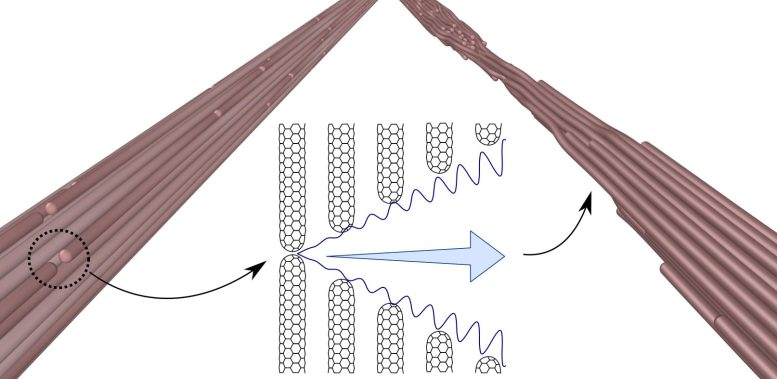
Rice University researchers found that cyclic loading of nanotube fibers leads to strain ratcheting that can eventually lead to the failure of the fiber. Credit: Illustration by Nitant Gupta and Evgeni Penev/Yakobson Research Group
Rice scientists calculate how carbon nanotubes and their fibers experience fatigue.
Up here in the macro world, we all feel fatigue now and then. It’s the same for bundles of carbon nanotubes, no matter how perfect their individual components are.
A Rice University study calculates how strains and stresses affect both “perfect” nanotubes and those assembled into fibers and found that while fibers under cyclic loads can fail over time, the tubes themselves may remain perfect. How long the tubes or their fibers sustain their mechanical environment can determine their practicality for applications.
A simulation shows the effect of axial stress on a carbon nanotube bundle over 10 cycles. Rice researchers calculate how cyclic strain and stress affect nanotubes and describe how fibers under cyclic loads can fail over time. Credit: Animation by Nitant Gupta
That made the study, which appears in Science Advances, important to Rice materials theorist Boris Yakobson, graduate student Nitant Gupta and assistant research professor Evgeni Penev of Rice’s George R. Brown School of Engineering. They quantified the effects of cyclic stress on nanotubes using state-of-the-art simulation techniques like a kinetic Monte Carlo method. They hope to give researchers and industry a way to predict how long nanotube fibers or other assemblies can be expected to last under given conditions.
“The time-dependence of an individual nanotube’s strength or endurance was studied long ago in our group, and now we’re contemplating its implications in the case of cyclic loading of the tubes and their fibers, or assemblies in general,” Penev said. “Recently, a couple of experiments reported that carbon nanotubes and
Rice University researchers determined several ways a nanotube experiences plastic failure, either through dislocation movement under 6% strain (here) or through shear band formation under 14% strain. Both mechanisms, seen in kinetic Monte Carlo simulations, only activate under extreme conditions, so neither appears to be a significant factor in fatigue of the nanotubes. Credit: Nitant Gupta/Yakobson Research Group
Perfect carbon nanotubes, considered one of the strongest structures in nature, tend to remain so unless some dramatic impact takes advantage of their brittle nature and cracks them into pieces. The researchers found through
Rice University researchers determined several ways a nanotube experiences plastic failure, either through dislocation movement under 6% strain or in this animation through shear band formation under 14% strain. Both mechanisms, seen in kinetic Monte Carlo simulations, only activate under extreme conditions, so neither appears to be a significant factor in fatigue of the nanotubes. Credit: Nitant Gupta/Yakobson Research Group